Talking to a plant engineer friend, he asked, “What’s the difference between PCI’s outage management software and our work management software?” A frequent refrain I hear when talking to folks, primarily because in our industry, we conflate words that seem to mean the same thing but aren’t precise. Even as a fleet outage coordinator, I’ve tripped myself! I want to walk you through the differences and similarities, keeping everything aligned, and even how to reduce your workload doing it.
To understand the differences, let’s start with this diagram:
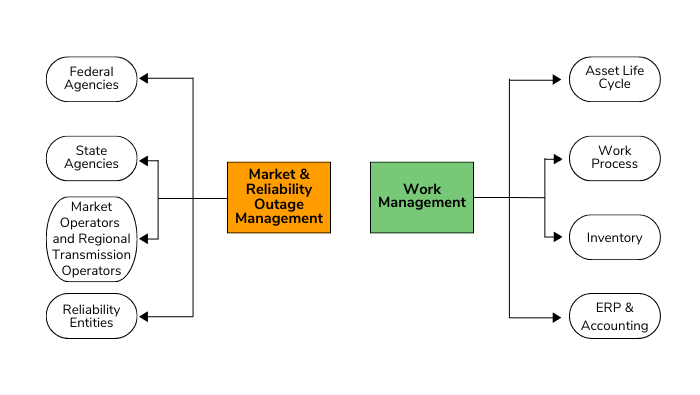
WMS and OMS Differences
The primary difference between the two systems is fundamentally linked to the objective each is trying to achieve. Market and Reliability Outage Management Systems (OMS) communicate the status of generation or transmission assets according to a set of defined and codified regulatory requirements. Work Management Systems (WMS) monitor and distribute data internally to the organization to monitor inventory, budgets, safety requirements, technical work schedules, and asset history.
The difference is evident in the entities that receive the notifications. In the case of OMS notifications, these are governed by two North American Electric Reliability Corporation (NERC) reliability standards, IRO-017 and TOP-003. These two standards generally lay out the requirements to communicate the generation and transmission equipment status that impacts the operation of a balancing authority area’s system. And while TOP-003 requirements merely reference the “Reliability Coordinator’s outage coordination process.” Conversely, WMS notifications and processes are beholding to internal corporate engineering and accounting committees defining frequency and reporting details.
Secondarily, the data flow for OMS data flows notifies and informs external entities of the work. In contrast, the organization uses WMS data flows internally to drive the outage work. Below are some of the different entities where information flows from both systems. Keep in mind that while the information’s names and specifics may differ from my experience, the same general rule for internal versus external applies.
Thirdly, the level of detail for an event is drastically different for each system. For example, a defined high level of detail is required for OMS outages. Conversely, work management systems typically contain significant quantities of technical data and multiple additional outage records that encompass the work performed on the asset. For example, an outage for the WMS may contain hundreds of work orders, inventory entries, and tracking details.
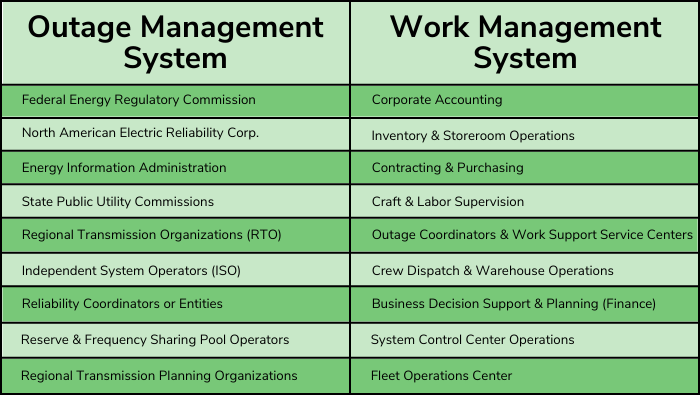
WMS and OMS Similarities
The fundamental similarities between the two systems boil down to the unit, event dates, and approval process flow. While both tools seek different objective outputs, the outcomes are identical, optimization of resources and efforts to maximize limited resources, whether reliable load service or maximizing unit availability. Therefore, electric utilities must align planning and approval workflows and streamline workloads to obtain the maximum return on investment for these complex systems.
Alignment and Reducing Workloads
Let’s be honest; every utility has the challenge of multiple systems and databases that purport to contain the same information. But unfortunately, the reality is something different. Ask any outage coordinator, and you’ll get an earful! Nevertheless, the two systems can stay synchronized and simplify communicating data throughout the organization by creating a tight data exchange and rules around that exchange. For example, creating a rule set and defined matrix of statuses will allow you to connect the Market and Reliability Outage record date, unit, and approval status with the Work Management outage master record date, unit, and status. Pushing changes between the two systems should initiate approval workflows and respect market and corporate accounting rules.
Great care should be taken to keep the rules and interfaces simple to avoid confusing the objectives of the two systems. Linking the two systems through an interface with reasonable frequencies will reduce the time spent verifying dates, inputting updates, and significantly reduce confusion in the system of record. Using the two systems with a reference key (either the OMS outage ID or the WMS outage ID) can simplify and expand the Plan-Do-Check-Act cycle, which enables teams to avoid recurring mistakes and improve processes. My experience is that expanded data access and relationships through the integration of the OMS and WMS systems have driven organizations to question the following:
- Eliminating outage season and hour shifting of maintenance schedules
- Leveraging existing utility personnel to reduce cost and build in-house technical expertise
- Reducing planning horizon and flexibility to take advantage of economic and opportunity outage periods
- Reconsidering in-sourcing and out-sourcing work activities with cost and risk in mind
- Risk management of capital spares and long-term service contract effectiveness
While necessarily different in their level of detail and intentions, OMSs and WMSs are married through data interfaces and comprehensive workflows. I’m hoping that with the help of this explainer blog post, you’ll find renewed benefits in implementing both systems.
If you’re interested in more information about OMS, contact us to request a case study or brochure.