Climate change is an unfortunate reality that very few scientists or world leaders dispute anymore. It’s rare for a scientific phenomenon to garner such universal consensus as the evidence is so clear and measurable. The facts point to greenhouse gases (GHGs) from human activity as the main culprit. The problem is complex and involves a wide array of activities, from agriculture, construction, industry, transportation, and power generation.
Electricity generation accounts for around 25% of total CO2 emissions and is considered the easiest to abate, but it is still disruptive and expensive. Revisiting nuclear power makes total sense to me but not to everyone. The DOE (Department of Energy) concurs and has made a $6 billion strategic investment through the Bipartisan Infrastructure Law (BIL). I say all that to remind myself why we’re discussing hydrogen as an electricity source. Like wind and solar a decade ago, it faces engineering, economic, and political headwinds. Similarly, it requires government subsidy and courageous business pioneers to build the foundation before it becomes profitable. It’s not a “no-brainer,” but big bets are being placed on it. It’s the path with the greatest potential to reduce carbon emissions across many industries at an acceptable cost and risk compared to alternatives. As energy professionals, it’s time to roll up our sleeves and work on the problem.
Today, hydrogen is mainly used in oil refining, ammonia, methanol, and steel production, and almost all come from splitting hydrocarbons that give off CO2. There are ways to capture and contain the CO2 underground, but that’s far from an ideal solution. Fortunately, we can also get hydrogen by splitting water directly with an electrical current that does not produce CO2 using electrolysis.

As you can see, little hydrogen is currently produced by electrolysis. Cost is a huge factor, although that’s changing rapidly for several reasons. Renewable energy costs are falling, and electrolyzers are becoming more efficient. Additionally, the skyrocketing natural gas costs make green hydrogen more cost-competitive. Electrolyzers are roughly 75% efficient, with new advances approaching 95%. Since a kilogram of hydrogen holds 39.4 kWh of energy, a 75% efficiency means it costs around 52.5 kWh of energy to create 1 kg of hydrogen. Australian company Hysata says its new capillary-fed electrolyzer cell slashes that energy cost to 41.5 kWh, which comes close to 95%.
Compare the efficiency of various power sources in our blog post: Power Plant Efficiency: Coal, Natural Gas, Nuclear, and More
The DOE’s “Hydrogen Shot” is part of the U.S. goal of net-zero carbon emissions by 2050. This initiative, launched in June 2021, “seeks to reduce the cost of clean hydrogen by 80% to $1 per 1 kg in one decade (“1 1 1″).” As you can see from the graphic below, we have a long way to go with costs today at around $5/kg.
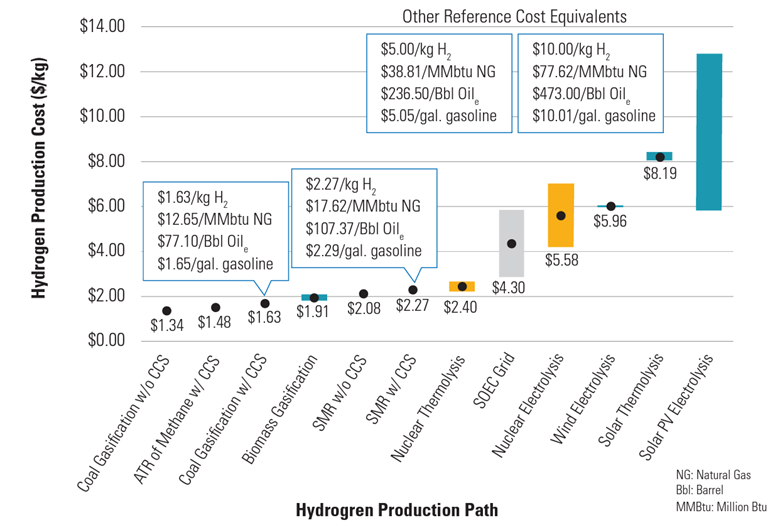
Another excellent and up-to-date resource for hydrogen pricing is the Platts Hydrogen Wall which graphically shows regional differences between hydrogen production prices using methods such as Steam Methane Reformation (SMR) and electrolysis.
Increasing the scale and capacity factor is key to lowering costs. Today, a large electrolyzer is 10 megawatts. At 75% efficiency, a 10 MW plant can produce 190 kg of hydrogen per hour (10/.0525). Sizes are scaling up very quickly as the technology and supply chain matures. A Danish company, Topsoe, expects to have a 500MW electrolyzer in service by 2024 with the ability to expand to 5 gigawatts.
Besides production costs, another common concern about green hydrogen is the water requirements. As you may have guessed, it is high, and depending on the amount of demineralization needed, water volumes can vary from 9-14 liters of water per kg H2 produced. Seawater and wastewater are viable options, although pre-treatment adds cost. However, desalination costs are not as high as you might suspect. According to a study by the professional services firm GHD, “to put the energy consumption for desalination into perspective, the energy demand for the desalination plant would be less than 0.5 kWh per kg of H2 produced (for a reverse osmosis plant), compared to around 50 kWh per kg of H2 for the electrolyzer.” For certain parts of the world, that’s very promising. Coastal areas with offshore wind farms, plentiful sun, and access to shipping could feasibly become hydrogen exporters to other parts of the world without those benefits. However, that brings up another challenge, which is compression and transportation. As my “Hydrogen Power 101” blog post mentioned, one of hydrogen’s greatest disadvantages is an extremely low volumetric density. Compression for storage or transportation is an energy-intensive process. Liquefication requires high pressure and cryogenic temperatures, which are costly. The DOE reports that delivery costs are approximately $8-$11/kg, depending on the method and volume of delivery.
Despite all the costs and challenges, I’m optimistic that adding electrolyzers to a portfolio of renewable resources is a net benefit. They are not as efficient as batteries for hourly storage, but they can have much longer runtimes than lithium-ion batteries and help diversify the portfolio. Even if we primarily use green hydrogen to replace existing dirty hydrogen for the industries they now service, it will help us reach our clean energy goals in a way few other alternatives can.
Request the slides from our webinar, The Path Forward for Green Hydrogen Production, to learn more about the hydrogen economy.